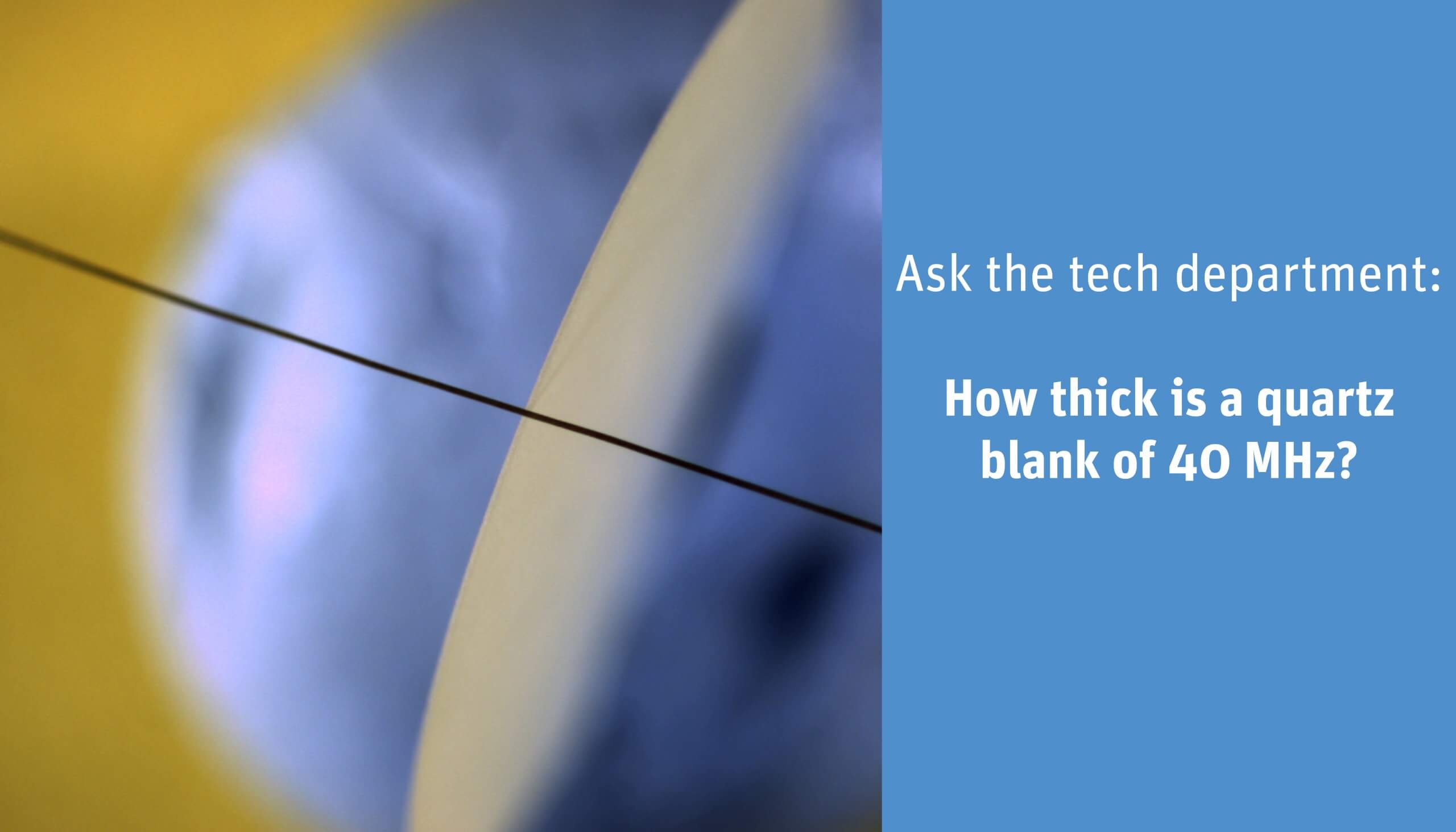
Let’s start this blog post with a little quiz: Guess for yourself – the solution will come in the text.
How thick is a quartz blank of 40 MHz? As thick as..
- A: a fingernail
- B: a normal sheet of printer paper
- C: one hair
Guess for yourself – the solution will come in the text. But first, let’s take a look at the theory:
Generally speaking, there is an inversely proportional relationship between the resonant frequency of a quartz blank and the thickness of a quartz plate.
In other words – the higher the resonant frequency is to be, the smaller the thickness of this quartz blank required for it. This is due to the fact that a so-called standing wave is formed between the interfaces of the quartz disk. This standing wave builds up inside the quartz wafer through reflection on the two interfaces of the transverse acoustic wave propagating in the thickness direction. The largest mechanical displacement is in the plane of the quartz plate perpendicular to the wave propagation direction.
At the resonant frequency, an odd number of half the acoustic wavelength fits in the thickness plane of the quartz blank. Therefore, the thickness of a blank is the main frequency-determining dimension of quartz produced in the AT-section. AT-section quartz crystals are commonly manufactured in the following frequency ranges:
- 1 MHz ~ 60 MHz, operation in fundamental mode
- 30 MHz ~ 250 MHz, operation in overtone mode (3rd; 5th; 7th; 9th overtone)
As mentioned earlier, the required thickness d of a quartz plate (blank) can be estimated since an odd number of half-wavelengths should fit in the thickness plane of the quartz blank.
In addition to the thickness of the quartz blank, the propagation velocity v of the acoustic wave in the quartz material must be taken into account in order to calculate the resonance frequency f. For AT-section quartz, the propagation velocity v is about 3320m/sec. Based on this, the required thickness d at a given frequency can be estimated as follows:
d ≈ n x ½ x v/f with n = 1, 3, 5,…
In the fundamental mode, the following thicknesses of a quartz blank will be obtained at the frequencies of 10.0 MHz and 40.0 MHz:
- 10.0 MHz ⇢ d = 166.0μm
- 40.0 MHz ⇢ d = 41.5μm
A quartz blank with a resonant frequency of 40 MHz is therefore a relatively thin disk. It has a thickness of only 41.5µm, which is about 0.04 mm. Thus, the thickness is about the diameter of a human hair and is about one tenth the thickness of a sheet of paper. So the correct answer was C. 😉
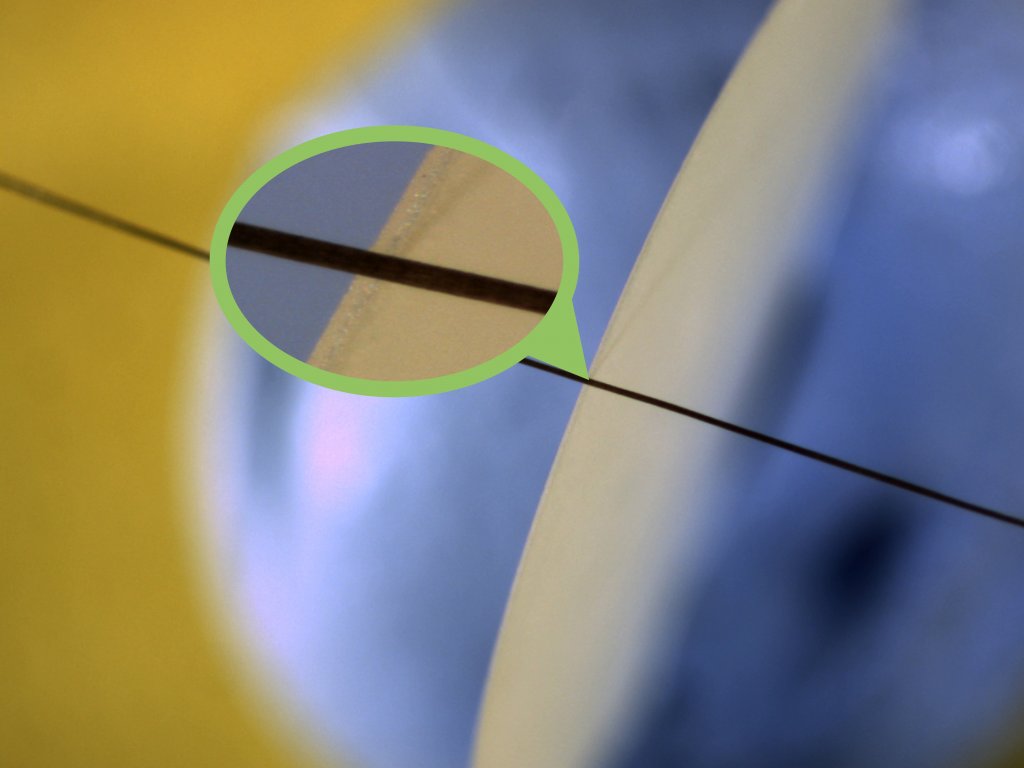
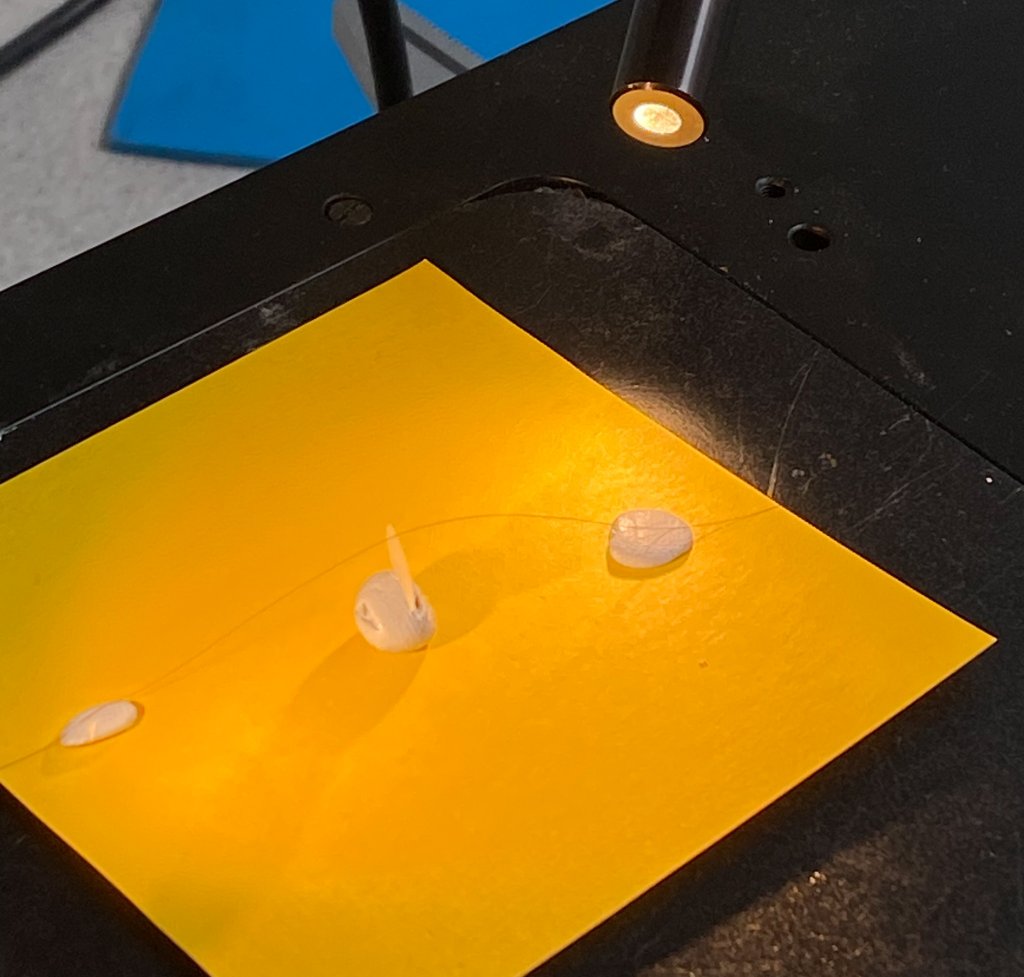
To give you a better idea of where the hair is in the picture and where the quartz blank is, here’s another look at the experimental setup:
And how can we now ensure, for example, that the tolerance of the resonant frequency deviates from the desired resonant frequency by only ±10 ppm (parts per million)?
If we translate this to the nominal thickness of the quartz blank, a deviation of the resonance frequency of +/-10ppm would correspond to a thickness tolerance of only +/-0.415 nm.
This is not achievable even with the most sophisticated mechanical operations. In addition, an oscillating quartz crystal is said to be a very low-cost component that will also be used in the consumer sector.
So how is this low frequency tolerance of only +/-10 ppm to be achieved?
Instead of the mechanical tolerance, which cannot be achieved in practice, we use a trick. This is because the resonant frequency of the quartz blank can be influenced in a very small range by coupling an additional weight.
To understand how this trick works it is important to know that the quartz blank can be excited to oscillate with the help of two electrodes. This only works because of the piezoelectric effect, which we will explain elsewhere.
The two electrodes on the opposing surfaces of the quartz blank have a very small mass, which in addition to the thickness of the blank affect the resonant frequency. For this reason, the quartz blank is made somewhat thinner than calculated, since the resonant frequency drops somewhat due to the additional coupled mass of the electrodes.
After applying the two electrodes by means of a sputtering process, the resulting resonant frequency should still be just above the final nominal frequency. In the last manufacturing step before the hermetic sealing of the quartz housing, the real “trick” then takes place.
It consists of applying yet another extremely thin metallic layer to the existing electrode. This is done using another sputtering process while continuously measuring the resonant frequency of the quartz disk. This second sputtering process is comparatively slow and is stopped as soon as the exact nominal frequency is reached.
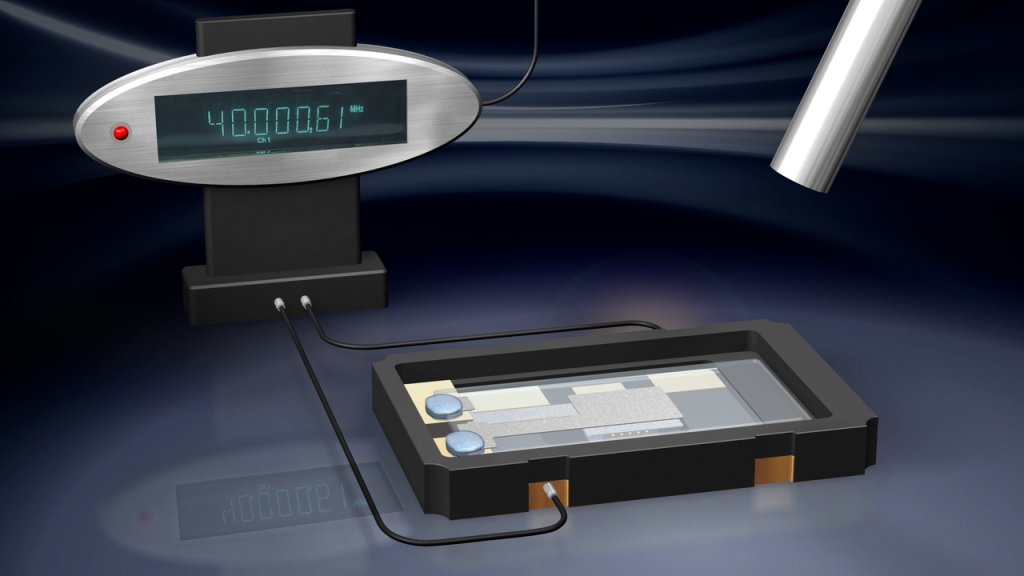
This “trick” of applying a very slight additional mass in a targeted and individually controlled manner allows the resonant frequency to be set very precisely, whereby a tolerance of the resonant frequency of +/-10 ppm or better can be achieved. This precision would not be achievable through purely mechanical machining steps.
Do you have any questions or need help choosing the right component for your circuit? Feel free to contact us.