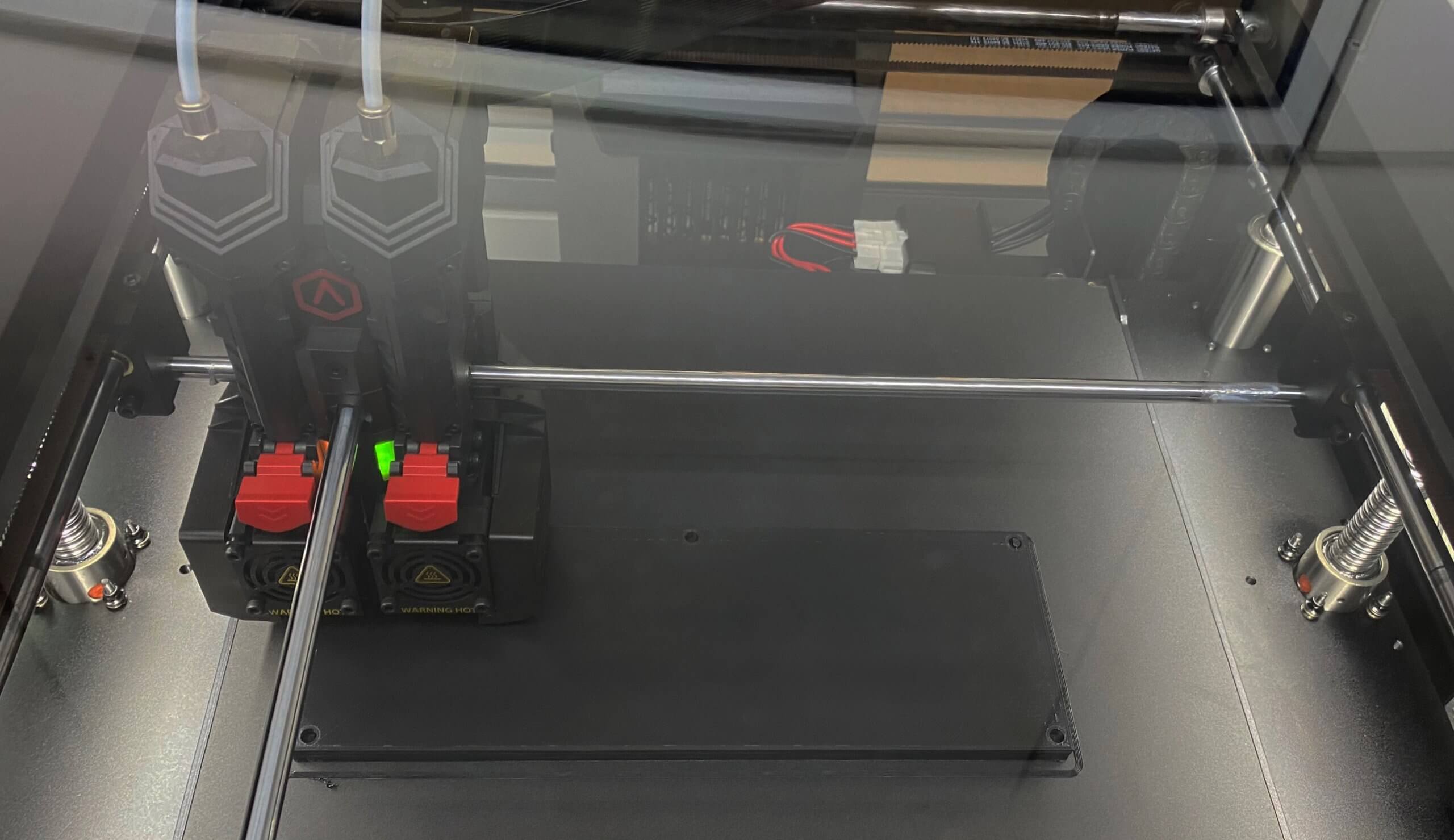
A new machine is improving our sample and prototype construction in Villingen-Schwenningen – although calling it a ‘machine’ may be stretching it 😊. Instead, what we have is a 3D printer, which brings a number of advantages: both our customers and our own in-house staff now benefit from greater speed and flexibility when it comes to producing prototypes and jigs or aids.
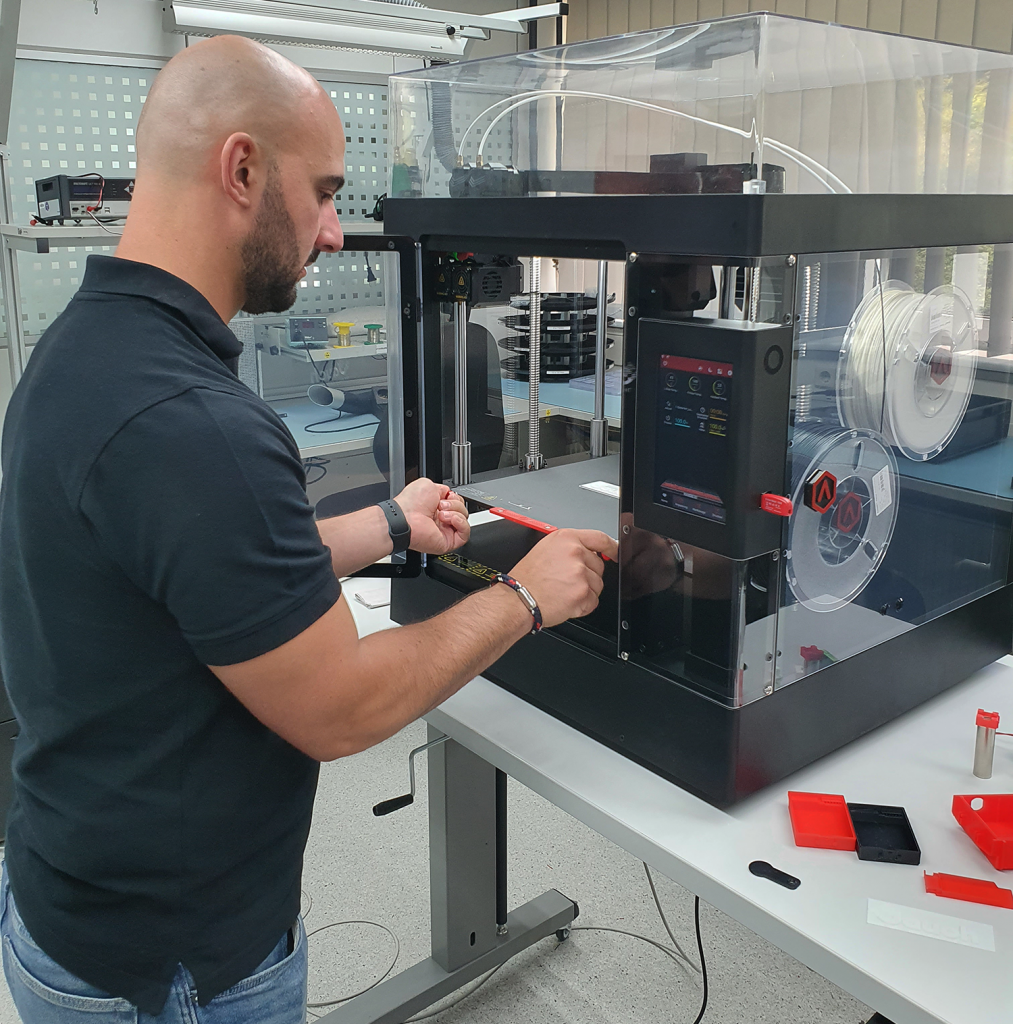
Creating workpieces with the 3D printer is also called ‘additive manufacturing’. As the name suggests, the workpieces are created by laying down the material at specific points layer by layer.
Ideal for creating prototypes
This 3D printer prints with what are known as ‘filaments’: thread-like thermoplastics wound onto rolls. Two print nozzles make it possible to work with two different plastics and use both for one printing. In our case, these thermoplastics are PLA and ABS. Using both has particular advantages when different material properties are required.
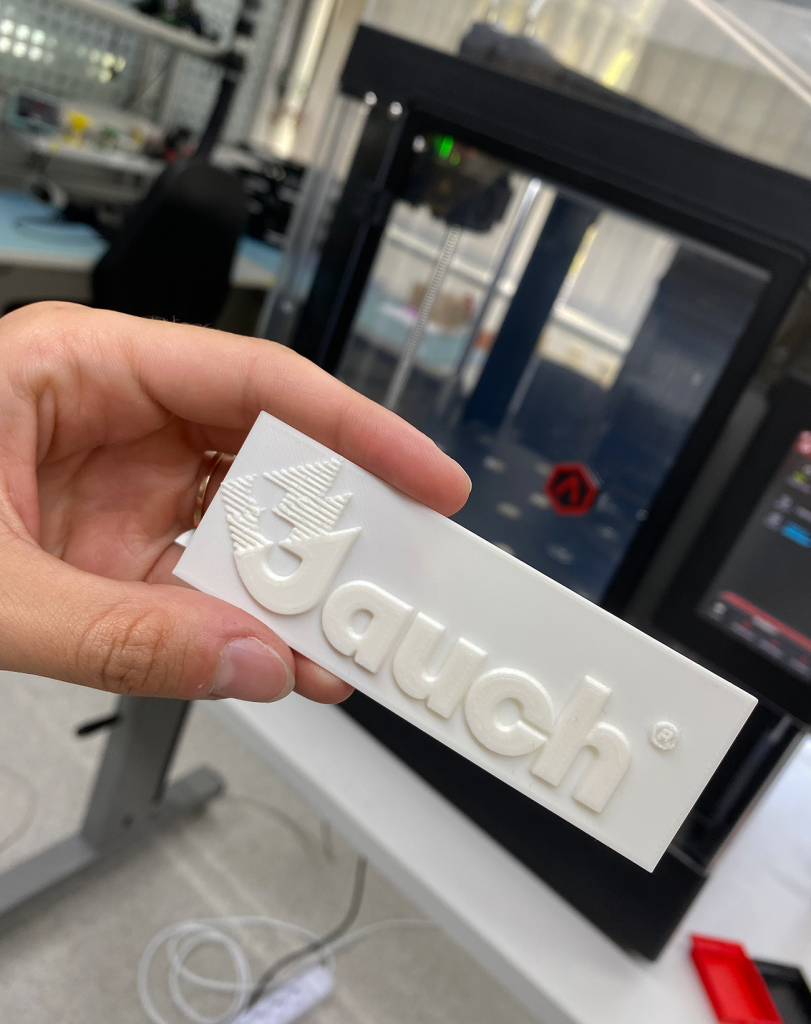
3D printers of this type are usually deployed for three main application areas, and this holds true here at Jauch as well. On the one hand, the printers can build prototypes quickly (Rapid Prototyping) to be able to test out functions or properties of the intended end product. They can also reproduce small-series production of end products (Rapid Manufacturing). And finally, they can create jigs and tools (Rapid Tooling).
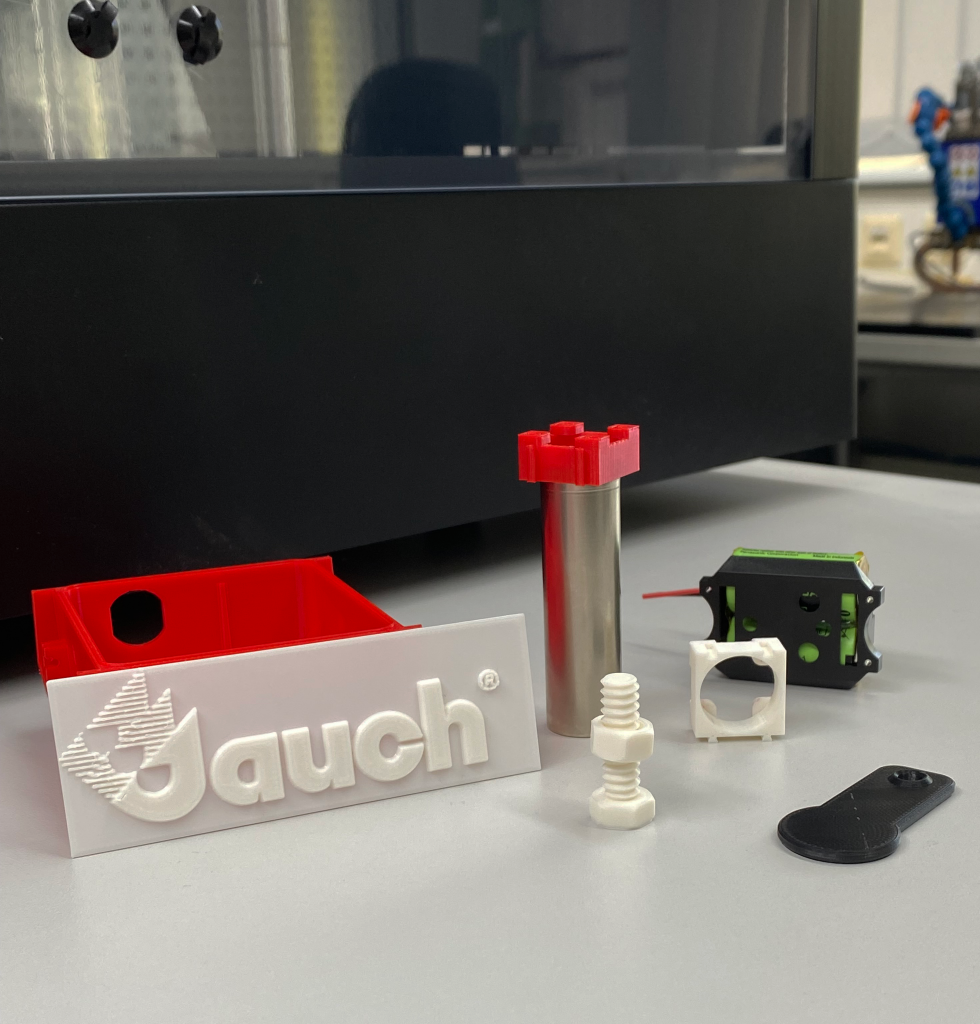
The advantages: speed and flexibility
Speed and flexibility are probably the two best-known advantages of 3D printing. As early as the development process, we can hand over the first prototypes to our customers and simply test things out. Small tweaks to the components can also be made quickly. Individual jigs that are needed to carry out the UN 38.3 transport test or the IEC certification can also be carried out promptly in this way. Individual fixtures required to perform the UN 38.3 transport test or IEC certification can also be quickly manufactured with the 3D printer.
Great article. 3D printer is a great invention.