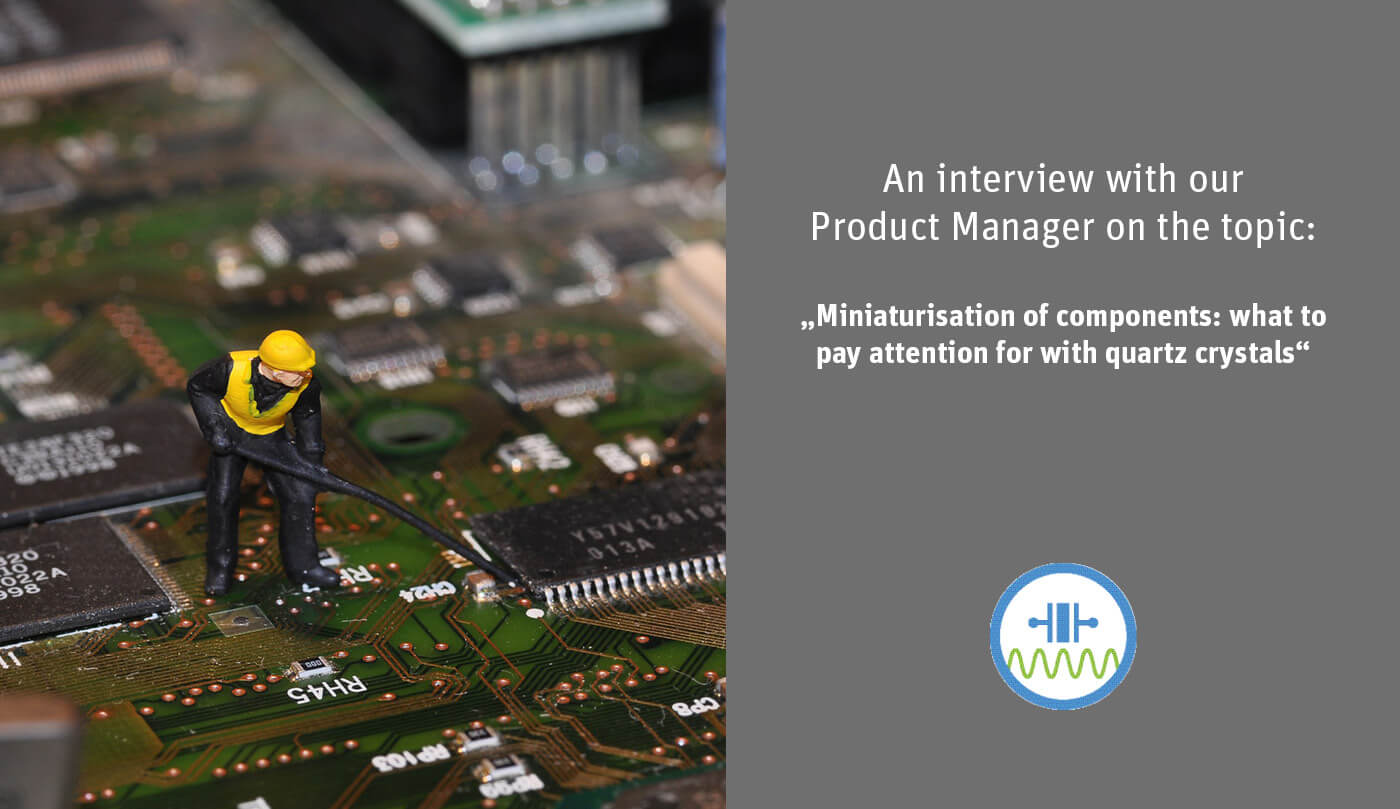
The topic of component shortage is omnipresent. Nowadays, almost every electronic component is affected. The reasons? There are various of them and they include supply problems, as well as, correspondingly, the availability of the components. Others can be traced back to digitization, resulting in an increased number of final products and, due to this, a higher demand. The situation is also unlikely to ease in 2022. Affected companies face the challenge of finding a solution as quickly as possible. Often, this means using components in other sizes or from other series.
To ensure that everything works as desired in the end, the new components must be installed correctly in existing circuits. Our colleagues from the technical support and product management deal with this topic intensively now.
We talked with our Project Manager, Leonie Weißer, about this topic.
What is the reason for the current situation?
Well, various reasons led to the component shortage. On the one hand, there were some discontinuations of ICs and packages by manufacturers, because they streamlined their product portfolios. The omnipresent trend towards even smaller components is one of the reasons for these discontinuations. However, incidents such as the fire at a Japanese IC manufacturer in October 2020, what primarily affected the production of TCXOs, also do not improve the situation.
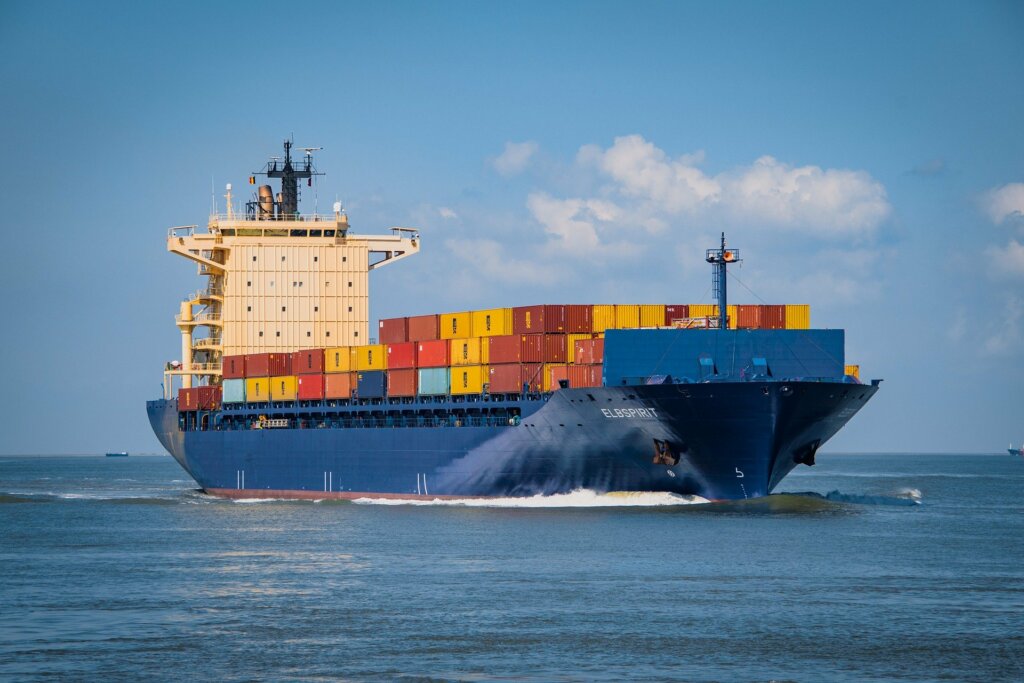
In addition, there are disruptions in the global supply chain caused by the pandemic. It was the air freight that suffered from the situation, resulting in a strong boost for shipping. And this in return, led to supply bottlenecks and price increases – also for primary materials.
After the slowdown, which has its origins in economic but also pandemic developments, in which many companies had to face a rather restrained ordering behaviour, demand rose sharply again. Even the reduced orders and delivieries of cases at the beginning of the pandemic did not ease the situation.
Hence, we notice a clear trend towards miniaturization in the market of frequency giving components, as with other electronic components, which first must be implemented throughout the entire value chain.
Therefore, the shortage currently coincides with the trend towards using ever smaller components – what impact does the miniaturisation of frequency giving components have on a customer’s circuit?
Basically, it can be said that the frequency of a quartz blank depends on the thickness or thinness of the blank. The thinner a quartz blank is, the higher is the frequency. However, this can lead to problems with the miniaturisation of components, since you need a thicker blank for lower frequencies. We meet physical limits when we try to put these thicker blanks in the smallest packages which would in return be needed for the final applications. This is a point which definitely has to be taken into account when switching to a smaller component.
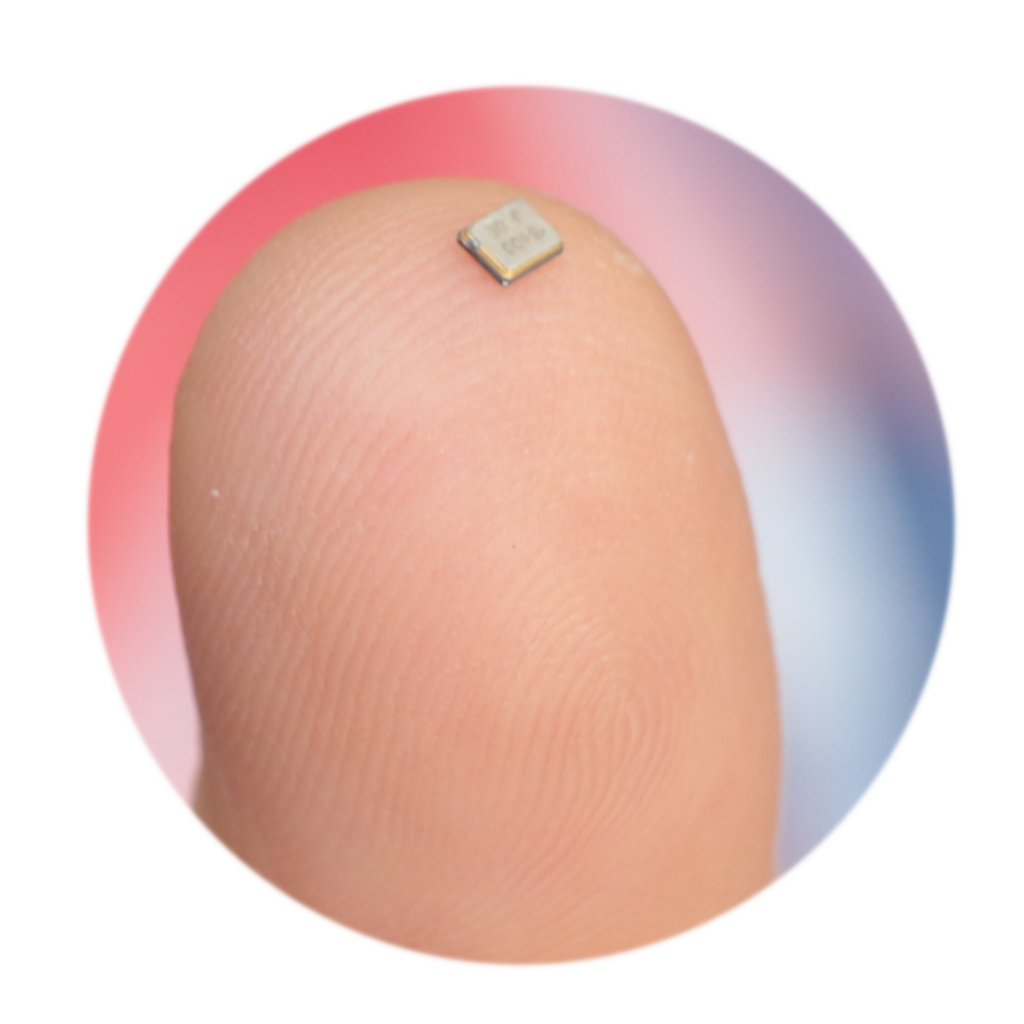
Apart from that, a current requirement for a frequency giving component is to ensure high frequency accuracy over a wide temperature range and, simultaneously, having a low power consumption. Since the output frequency depends on many different factors in the customer’s circuit, for example the load capacity, we recommend a close exchange with our sales department in order to select the appropriate component for the corresponding application.
What does that mean for you and your colleagues?
We receive many inquiries in which our customers describe problems with their circuit. Next, we identify these problems. Often, this requires circuit analyses to be carried out. In the cases when other components are used, a re-design of the circuit may be necessary. We provide support here, too.
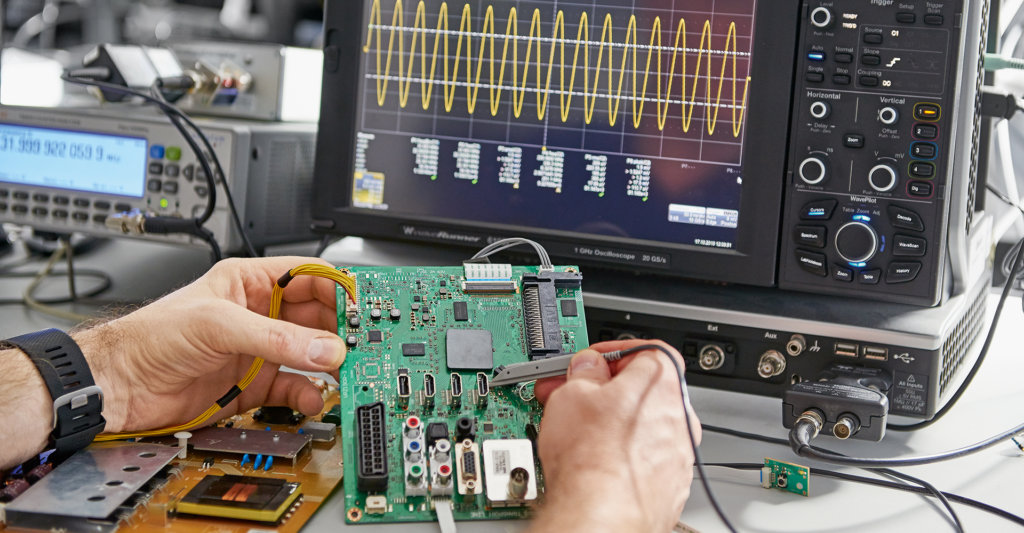
We do everything we can to ensure availability for customers and prevent line stoppages. Here, the close contact to our suppliers is helpful. As a manufacturer, we can also rely on long-standing and stable relationships here.
The cooperation with our customers is close and based on open communication. We look after our customers from development to technical support. During the hard time of the pandemic situation, we were also able to win new customers and to convince them with our technical advice and intensive support. This makes us particularly happy. Especially now, against the background of component discontinuations and delivery difficulties, it is important for a successful project to act early and quickly.
What points need to be considered during a re-design?
In the re-design process, more or less exactly the same points have to be considered as with a new design of a circuit. It is essential, that the quartz crystal resonates in the circuit. Since the miniaturisation of the package. Smaller quartz crystals almost always have a higher resonance resistance. Simply inserting them in the existing circuit means that the quartz may no longer resonate correctly or, in the worst case, not at all. However, this can be solved by adjusting the circuit, for example by reducing the load capacities and adjusting the resistors.
If new components are used in an existing circuit, the drive level must also be analysed. The drive level describes the power acting on a quartz crystal. The maximum value is defined in the data sheet and must not be exceeded. This is to avoid an overload of the quartz.
The problem is that a higher drive level is required due to the higher resonance resistance and the smaller case sizes. However, a high drive level is reflected in the lifetime of a quartz. A balance between the required lifetime and the vibration safety is therefore essential.
Finally, it should be noted that the measurements of the circuit must also be rebuilt when other components are used. Otherwise, values show up distorted.
I would also like to point out that there is not the one way to re-design circuits and often different options work. Sound technical advice helps to find a suitable solution. My colleagues and I are gladly available for this.
In which other topics do we support our customers further?
We support our customers not only in the selection of the appropriate frequency giving component, but also in topics such as the circuit optimization or support with the design-in of components. In our electronics laboratory in Schwenningen, we carry out customer-specific circuit analyses, as previously explained. In doing so, the points described in this interview can be checked. Specifically, this includes frequency accuracy, vibration safety as well as corresponding changes to the layout.
Are you also facing the problem of re-design? Feel free to contact us and together we will find a solution for your project.
The interview was taken with Leonie Weißer, Product Manager at Jauch Quartz.